le paratie sono state avvitate |
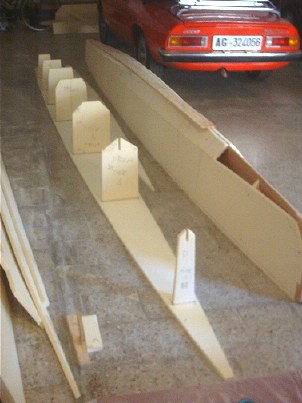
|
montaggio delle paratie alla
coperta |
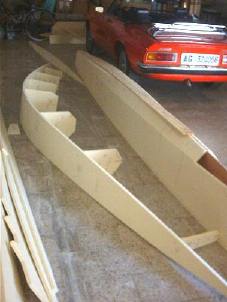
|
particolare della prua
dell'amas |
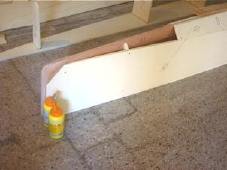
|
quartabuonare le striscie
intermedie
|
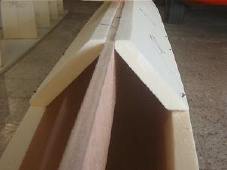
|
la chiglia da piatta diventa a
spigolo |
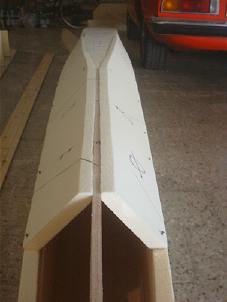
|
lo scafo ancora a spigolo |
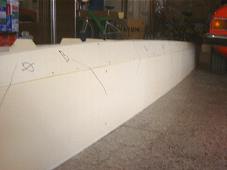
|
l'opera morta dell'amas
laminata in piano |
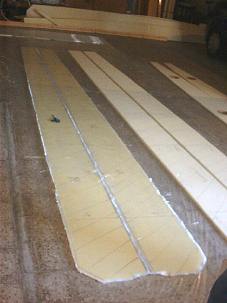
|
si stende il tessuto
direttamente dal rotolo
|
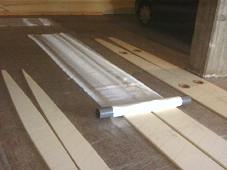
|
una porzione di tessuto
già steso viene laminata |
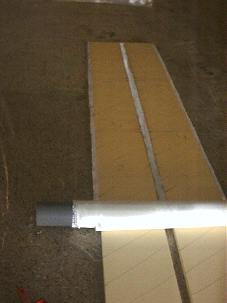
|
viene strappato il peel-ply
dalla superficie interna della traversa |
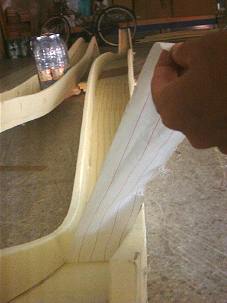
|
montaggio delle traverse |
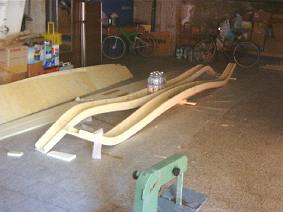
|
inserimento rinforzi in
compensato per i bulloni di fissaggio allo scafo centrale |
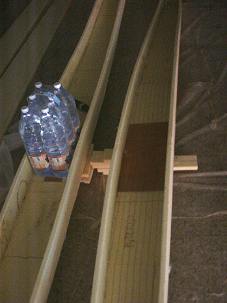
|
chiusura della traversa
|
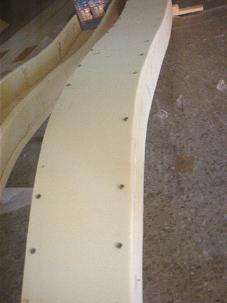
|
rinforzi in legno |
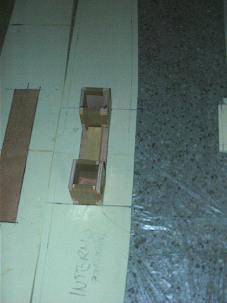
|
chiusura traverse |
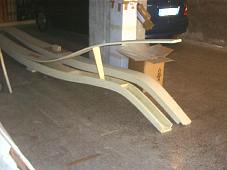
|
prima prova di montaggio della
traversa sullo scafo centrale.
|
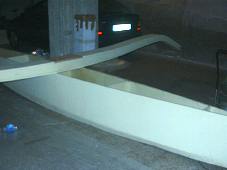 |
taglio della coperta
utilizzando il progetto in scala 1/1 |
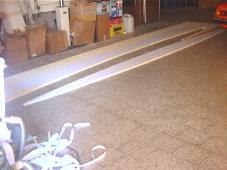
|
taglio della coperta
utilizzando il progetto in scala 1/1 |
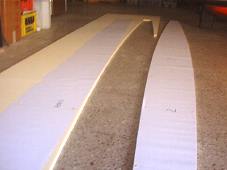
|
per tenere ferma la sagoma di
carta, semplici puntine da disegno |
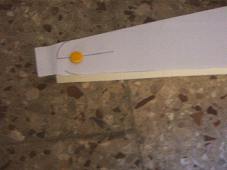
|
il dritto di prua e parte
della chiglia in compensato di okume
|
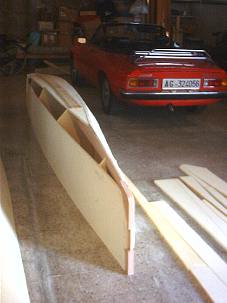
|
il dritto di prua deve essere
ancora sgrossato e rifinito. la fiancata sinistra è gia montata
a secco |
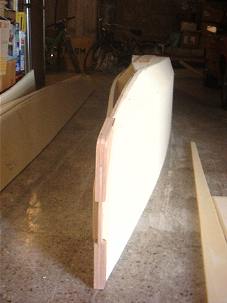
|
il listello di legno avvitato
sul fondo piatto serve a
migliorare la curva della chiglia quando si laminerà l'interno
dello
scafo. |
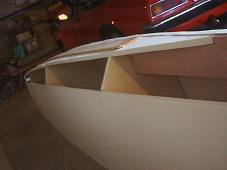
|
incastro nel dritto di prua
del pvc con il compensato. |
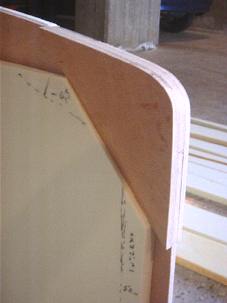
|